UNITED KINGDOM – Egger, a top wooden panel manufacturer, and Wren, a leading kitchen furniture manufacturer, have implemented a closed-loop waste management system as part of their ongoing commitment to sustainability and waste reduction.
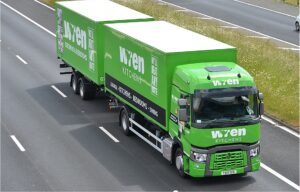
This innovative partnership not only minimises environmental impact but also enhances operational efficiency.
As part of the circular initiative, Wren collects offcuts and waste MFC (melamine faced chipboard) material from its manufacturing facilities in Howden, Scunthorpe, Barton, and Parrot Street. These materials are returned to Egger’s production facility, supporting a sustainable process that benefits both businesses and the environment.
In line with their focus on reducing ’empty road miles’ and fostering a sustainable future, Wren loads palletised waste MFC material onto trucks for transport to Timberpak Washington. There, the material is unloaded, segregated, and processed for reuse. This processed waste wood is then integrated into Egger’s particleboard production at Hexham.
To maximise efficiency, Wren’s trucks proceed from Timberpak Washington to Hexham, where they collect finished chipboard for return trips, optimising transport by eliminating empty loads. This approach reduces waste disposal costs, minimises transportation emissions, and strengthens the circular production cycle.
By reusing offcuts and waste MFC materials, Egger significantly reduces reliance on virgin resources, making their manufacturing process more environmentally friendly. This closed-loop system exemplifies the principles of a circular economy, transforming waste into a valuable resource and demonstrating how collaborative initiatives can achieve mutual benefits.
“The collaboration between Egger and Wren highlights the immense potential of closed-loop waste management systems to reimagine waste as a useful material,” said a representative. “This integration of waste back into the production cycle showcases the tangible benefits of circular economy principles.”
0 Comments